Six Sigma versus TQM
Comparison and Overview of Six Sigma and TQM
Six SigmaOpens in new window represents a new wave of the quality management evolution (preceded by TQM evolution) toward operational excellence.
- The definition of TQMOpens in new window is different from that of Six Sigma, but the aims are similar.
- Six Sigma has additional data analysis tools and more financial focus than what is found in TQM.
- TQM has a comprehensive approach that involves and commits everyone in a company, while Six Sigma has a project management approach that is associated with a team.
Arnheiter and Maleyeff (2005) have indicated that a number of components of Six Sigma can be traced back to TQM. This explains that Six Sigma is an extension of TQM and that they both share similar principles. Snee (2007) suggested that there are benefits for integrating Six Sigma with the Baldrige assessment (a TQM model) and ISO 9000Opens in new window.
Antony (2004) stressed that it is important to remember that Six Sigma has a better record than TQM since its inception in the mid-1980s.
Tables X-1 and X-2 represent a summary of a literature review on the Six Sigma and TQM similarities and differences, respectively. Based on an extensive literature review (Yang; 2004 for example) and the authors’ own experience, a comprehensive and appropriate basis for comparison based on 25 dimensions is considered here.
Table X-1 Similarities and Relationship of Six Sigma and TQM | ||
---|---|---|
Dimension | Six Sigma | TQM |
Theory | Similar to TQM in terms of theory & handling methods (Hwang 2006) | Both draw from behavioral and quantitative sciences (Friday-Strout and Sutterfield 2007). |
Focus (on customer and process) | Six Sigma has a stronger emphasis on customer satisfaction through mainly focusing on critical to quality (Klefsjo et al. 2001 and Schroeder et al. 2008) | TQM and Six Sigma share same values such as process focus, customer focus, CI, and use of facts and data (Tannock et al. 2007). Customers are in the focal point of TQM (Voros 2006). Both focus on product quality and quality assessment (Cheng 2008) |
Management support | It has better success obtaining support (Montgomery 2001) | TQM puts less stress on the support by management and financial department (Hwang 2006). Both depend on it. |
Basis | It includes two dimensions of philosophy (or management) and methodology (or analysis) (Hwang 2006) | TQM can be described as a philosophy and is considered as a management process that applies management principles (Jitpaiboon & Rao 2007) |
To be continued ... |
Table X-1 Continued. Similarities and Relationship of Six Sigma and TQM | ||
---|---|---|
Dimension | Six Sigma | TQM |
Aim | It is an improvement methodology (Hoerl 2004). Six Sigma and TQM focus on CI (Antony 2006) and share similar principles and aims | TQM aims at improving all processes within an organization, and it treats the organization as a total system (Shah and Ward 2007). It is a holistic Quality Management System or management process with the goal of generating a quality-based culture (Aly et al. 1990) |
Link to Deming | DMAIC is closely linked to PDCA cycle (Haikonen et al. 2004; Linderman et al. 2006), and it improves upon the PDCA cycle (Tannock et al. 2007) | TQM is based on teachings of Deming (Snee 2004) in which the main tenets of Six Sigma are embedded (Maleyeff and Kaminsky 2002; Black and Revere 2006) |
Change | Six Sigma is focused on belts leading the projects with the involvement of the team members | TQM and Six Sigma use training and organization-wide support as levers of change (Buch and Tolentino 2006) |
Approach to design | Its design process is more prescriptive (Schroeder et al. 2008) as it uses the DMADV or DFSS which provide stronger focus on product design (Upton & Cox 2008) | TQM and Six Sigma stress the important of using QFD and cross-functional design and design for manufacturability (Schroeder et al. 2008) |
Complexity | It is criticized for the difficulty to stick with the rigor of the approach (Linderman et al. 2006) | Top managers often find it difficult to understand TQM, and it does not work well for processes that require major changes (Klefsjo et al. 2001). It is very difficult to manage or evaluate as it evolved to become so all-encompassing and intangible (Jitpaiboon and Rao 2007) |
It is seen from Table X-1 that Six SigmaOpens in new window and TQMOpens in new window share common ground in terms of theory, philosophical approach, CI focus, aims, principles, links to the teachings of DemingOpens in new window, approach to design, focus on customer, focus on process, dependence on management support, change approach, and complexity.
On the other hand, Table X-2 (briefly below) represents that Six Sigma and TQM are different in terms of mutual relationship (Six Sigma can be seen as an expansion for and a part of the holistic TQM which in its turn can help Six Sigma), financial focus and scope, incentives and career development, strategic link, project selection approach, training focus and intensity, team approach, structure, progress monitoring, basis for motivation, tools, performance target, focus on suppliers, and record of results.
Table X-2 Differences and Relationship of Six Sigma and TQM | ||
---|---|---|
Dimension | Six Sigma | TQM |
Strategic link | Six Sigma provides better alignment with organizational strategic business objectives (Antony 2006) | A CEO considers TQM as quality slogan carried without translated goals to implementable initiatives (George 2002) |
Mutual relationship | Six Sigma is an expansion of TQM (Terziovski 2006) with components traced back to TQM (Aly et el. 1990; Arnheiter and Maleyeff 2005) and can be viewed as a methodology within TQM and not as an alternative (Klefsjo et al. 2001) | Six Sigma is an extension of TQM. Existing TQM activities can help in the implementation of a Six Sigma system (Cheng 2008). TQM has become an umbrella for Six Sigma and other tools (Harnesk & Abrahamson 2007) |
To be continued. |
Table X-2 continues Differences and Relationship of Six Sigma and TQM | ||
---|---|---|
Dimension | Six Sigma | TQM |
Financial savings | It tracks cost savings on a project-by-project level (Schroeder et al. 2008). It has more financial focus (Kwak & Anbari 2004) | It has an organization-wide calculation for COQ (organizational-level tracking) (Schroeder et al. 2008) |
Project selection | Project selection rights reside with management to ensure financial and strategic implications are considered (Schroeder et al. 2008) | There is no clear way of prioritizing projects that are carried out irrespective of cost to operation (Banuelas & Antony 2002). The link between economy and project selection was missed in most TQM implementations (George 2002). Projects can be selected by bottom-up approach which is often based on convenience (Schroeder et al. 2008) |
Training focus | It is a structured training focused on Belts or levels (Basu 2004) that create an infrastructure for implementation (Terziovski 2006) without focus on wide team participation (Schroeder et al. 2008) | It is a comprehensive approach that involves everyone (Anderson et al. 2006) using improvement teams that are sometimes in the form of a quality department (Schroeder et al. 2008) |
Functional team | It uses an intraorganizational cross-functional team for CI (Cheng 2008) | It uses an interorganizational team for CI (Cheng 2008) |
To be continued. |
Table X-2 continues Differences and Relationship of Six Sigma and TQM | ||
---|---|---|
Dimension | Six Sigma | TQM |
Criticized for | It is criticized for not focusing on all people and culture (Linderman et al. 2006). However, it is less difficult to reengineer, restructure, and evaluate breakup of an organization using Six Sigma as the team is more independent of the process under consideration (Hwang 2006) | Terziovski (2006) indicated that Snee claims TQM does not integrate human elements of improvement like teamwork as good as in Six Sigma |
Incentives | It has less challenge to have incentives to pursue improvement (Terziovski 2006) | There is less incentives and career development focus in TQM (Upton & Cox 2008) |
Motivation | Its motivation is inspired by tangible benefits (Motwani et al. 2004) | It is driven by idealism of quality (Motwani et al. 2004) |
Training intensity | There is more intensity in the training of full-time improvement individuals (Schroeder et al. 2008) | TQM uses shorter length for training (i.e., 1 week) but targets all people in the plant (Schroeder et al. 2008) |
Structure | It is a project-focused approach using DMAIC, reinforcing Juran tenets (Basu 2004) and a well-structured DMAIC road map for deployment (Terziovski 2006). A key strength in it is that it builds at QI structure in parallel with existing management structure (Linderman et al. 2006) | TQM is not sequential, and it does not have a specific route used by all organizations no matter what their cultural circumstances look like (Leonard & McAdam 2004). TQM is criticized for lack of clear definition or strategy and structured communication (Ricondo & Viles 2005) |
To be continued. |
Table X-2 continues Differences and Relationship of Six Sigma and TQM | ||
---|---|---|
Dimension | Six Sigma | TQM |
Progress monitoring | It has a mix of long- and short-term focus with better monitoring of progress toward goals (Motwani et al. 2004) | It promotes open-ended and open-financed continous QI (Klefsjo et al. 2001). It has a long-term focus with loose monitoring of progress toward goals (Motwani et al. 2004) |
Tools | It is not new in terms of the tools and techniques, but it has a new deployment approach to process improvement (Banuelas & Antony 2002). It has additional data analysis tools with more statistical emphasis (Basu 2004). It is criticized of focusing on tools more than problems (Linderman et al. 2006) | TQM and Six Sigma attempt to find root causes, but TQM is not as specific or focused (Klefsjo et al. 2001). It has mainly seven quality and seven management basic tools (Arnheiter & Maleyeff 2005) |
Performance target | Six Sigma performance target applies to a single critical quality characteristic (Banuelas & Antony 2002). Sigma level can be used to assess quality level attained and can be used in benchmarking (Klefsjo et al. 2001) | It has a more comprehensive performance target which applies to the total product (Banuelas & Antony 2002). TQM does not have a specific way to quantify quality level attained by an organization (Klefsjo et al. 2001) |
Suppliers | Six Sigma target supplier only if they are critical to quality at process under investigation (Schroeder et al. 2008) | A vital element of TQM is targeting supplier management (Schroeder et al. 2008) |
Results | Six Sigma has a better record than TQM since its inception in the mid-1980s (Antony 2004), a better record of effectiveness (Cheng 2008) and is better focused (Montgomery 2001) | Some researchers found a significant impact of TQM practices on operational performance, and others did not (Shah & Ward 2003) |
Conclusion
TQMOpens in new window and Six SigmaOpens in new window are very powerful customer intelligene (CI) methodologies that share common grounds in terms of principles, goals, customer and process focus, dependence on management support, approach to design, approach to change, and complexity.
On the other hand, they are different in terms of mutual relationship, financial focus, training focus, incentives, strategic link, project selection approach, team approach, structure, motivation, tools, performance, and record of results.
However, these differences can be considered as additional strengths for the integration of TQM and Six Sigma as the weaknesses of one are completed by the strengths of the other.
Despite their differences, there are many areas where TQM and Six Sigma intersect and there are compatible areas where one of them may excel forming an opportunity to help the other one. Thus, the integration of the two is concluded to be possible and beneficial.
Also, TQM and Six Sigma were presented as part of a framework for customer intelligence (CI)Opens in new window. TQM can be holistic and comprehensive umbrella that reaches to all stakeholders, and Six Sigma can be the extension that provides a strong structure for achieving greater quality improvements (QIs).
See Also:
- Research data for this work have been adapted from the manuals:
- Schroeder, R. G., Linderman, K., Liedtke, C., & Choo, A. S. (2008). Six Sigma: Definition and underlying theory. Journal of Operations Management, 26, 536 – 554.
- Anderson, R., Eriksson, H., & Tortensson, H. (2006). Similarities and differences between TQM, Six Sigma and Lean. The TQM Magazine, 18 (3), 282 – 296.
- Salah, S., Carretero, J. A., & Rahim, A. (2009). Six Sigma and Total Quality Management (TQM): Similarities, differences and relationship. International Journal of Six Sigma and Competitive Advantage, 5 (3), 237 – 250.
- Klefsjo, B., Wiklund, H., & Edgeman, R. L. (2001). Six-Sigma seen as a methodology for total quality management. Measuring Business Excellence, 5 (1) 31 – 35.
- Terziovski, M. (2006). Quality management practices and their relationship with customer satisfaction and productivity improvement. Management Research News, 29 (7), 414 – 424.
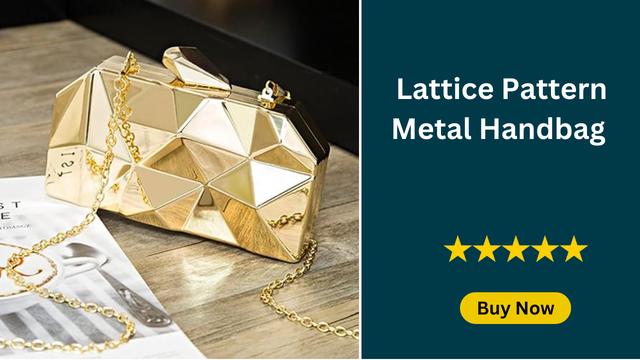